

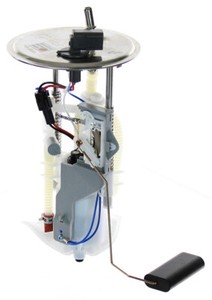
The fuel line was completely bled down to zero psi. This is the voltage signal from the FRP sensor on a 2005 Expedition. If the fuel pump fuse blew, or the inertia switch tripped, the FPDM will not power up and the PCM will store those codes.Īn oscilloscope tapped into the FRP signal lead can provide some fast and useful information about the fuel pump’s performance. So, if you get one of these vehicles with no fuel pressure, and you see the fault codes P1233 and/or P1234 (Fuel Pump Driver Module Disabled or Offline), don’t be so quick to assume the FPDM has failed. One thing to keep in mind is that, currently, the same battery positive feed used to supply the fuel pump is the same power feed used to operate the FPDM. Beware, some scanners may display the readings in the yellow column, so know your tool. The green column reflects the fuel pump monitor PID on a scanner. As you can see by the chart, that would send you in completely the wrong direction. For example, a 75% duty signal could be misread as 25%. Depending on your setting, your readings could get reversed. Be mindful of the trigger setting on your tool. The yellow column represents the duty cycle that you may see if you tapped into the FPDM monitor circuit to the PCM with a duty cycle meter or an oscilloscope. However, as simple as that may sound, reading them requires knowledge of your own tool.
.jpg)
There are only three diagnostic monitor signals that the FPDM will return to the PCM. So you not only get to look at the system from the PCM’s “eyes,” you also get to see it through the FPDMs “eyes” too. The nice thing about diagnostics on this system is that you have two control modules that are both reporting diagnostic information. Any of those signals from the PCM will result in zero fuel pump operation. The PCM will not send those duty cycles unless something has gone terribly wrong inside the PCM, or unless a technician commands the PCM to send those duty cycles via a suitable scan tool. As for the duty cycles that fall between the cracks - 0% to 4%, 51% to 67%, and from 82.5% to 100% - they are invalid. However, the FPDM will accept 67.5% to 82% as a valid “off” command. If the PCM wants the fuel pump turned off, it will send a 75% duty cycle to the FPDM. For example, a duty cycle from the PCM of 20% will equal 40% of fuel pump full-on, and a duty cycle of 50% would equal 100% of full-on at the pump.

Whatever the PCM’s duty cycle is, multiply that by “2” and that is the fuel pump’s on percentage. In this range, the fuel pump output is directly proportional to the fuel pump’s “on” time. Between 5% and 50% duty cycle is the normal range of demands from the PCM to the FPDM. To achieve its goal, the PCM communicates a duty cycle to the fuel pump driver module (FPDM). The fuel pump relay is now toggled by the ignition switch. One notable change however, is the PCM no longer controls the fuel pump relay. One Ford-specific component that still remains after more than two decades is the inertia fuel cut-off switch. A couple of things that become optional across other makes that Ford still includes are the fuel pump relay and the in-line fuel filter. This much should remain the same for any electronic returnless system. This system consists of a rotary vane fuel pump (same as before), fuel line (pressure only), fuel rail pressure sensor (that also contains a temperature sensor), fuel pump control module and, of course, the PCM. With an electronic returnless system, the PCM can now raise or lower fuel pressure at will. Also, making it electronically pressure controlled gives the PCM more flexibility over fuel control by adding another option if needed. As an additional benefit, a returnless system, having one less fuel line, reduces the chances of a fuel leak.
